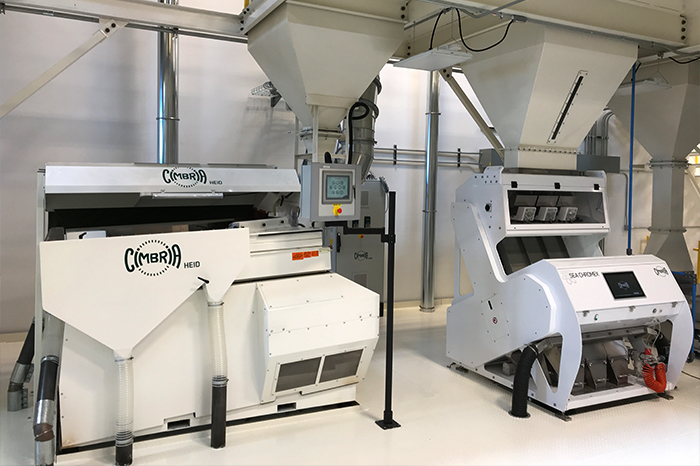
If your processing facility isn’t utilizing a high-quality color sorting machine, you may be missing out on an indispensable piece of technology that can boost both production capacity and product quality in your operations. Modern color sorting machines eliminate the need for time-consuming and inefficient manual sorting and also handle complex sorts not capable of traditional mechanical separations like air screen cleaners, gravity tables, destoners and indents. These machines have the ability to enhance the efficiency, accuracy, and quality or your cleaning lines. There are several models to choose from to match a variety of seed, food, grain, feed and milling applications and plant capacity.
Many industries, particularly agriculture and food processing, find color sorters integral to their operations due to the ability to remove dangerous foreign materials like glass and stones. These machines can sort through several different kinds of material at rapid speeds.
How Do Color Sorters Work?
Color sorters, also called optical sorting machines, have made a transformative impact on seed and grain processing plants. They are able to identify the characteristics of the raw material going through the machine and separate it based on color, size, quality and kernel defects. Non-conforming grain is ejected from the good product along with foreign materials like other grains, rocks and glass. Defective material is anything with impurities like discolored pieces, foreign objects, damaged seeds, or diseased grains. Removing these types of foreign materials with an optical sorter can increase the lifespan of downstream equipment while also ensuring a safe finished product.
Most color sorters use multiple types of high-definition cameras to look at kernels in the visible spectrum like human eyes, but also in wavelengths beyond what human eyes can see to make more difficult separations. One example would be a dark colored grain and a dark stone that to the human eye have the same color, cameras that see in a spectrum beyond the human eye can differentiate this and remove the stone. The cameras in color sorting machines can be programmed to utilize various sorting criteria: color, size, shape, texture, disease and insect damage are some common examples. The imaging technology is so accurate that the cameras can be fine-tuned to the exact color the product should be and quickly get rid of product that doesn’t match which is very helpful when consumers expect a uniform product.
Modern Color Sorters vs. Traditional Methods
Years ago, before widespread use of automated machines, all sorting was done by hand. As you can imagine, this manual process was incredibly time-consuming, inefficient, and inaccurate. Machines to sort grains mechanically were the next evolution in efficiency and quality for conditioning plants and these are still manufactured and used in plants around the world today. Examples of these mechanical separation machines include air screen cleaners, indented cylinder separators, gravity tables and destoners to name a few. Modern plants have enhanced the quality and efficiency of their mechanical separations by either adding color sorting machines as a new step in their existing process flow, or with some grains by replacing mechanical separators altogether to increase product quality and decrease operating costs. Color sorting technology catches imperfections that human eyes would not, ensuring a completely consistent product quality shift after shift, day after day and adds a sorting tool with vision that mechanical separators cannot achieve.
Maintenance & Upkeep
As with any machine, color sorters need to be maintained properly to continue running at peak performance. General lack of cleaning or maintenance can cause even the best quality color sorter to decline. Standard maintenance is crucial to protect your investment and keep your operation running smoothly.
It’s important to keep all components of the sorter clean and mechanically maintained. Dust filters need to be checked and cleaned on a regular basis. Another way to increase the longevity of your machine is to monitor the air quality coming from the compressor. If you find the compressed air is full of moisture, oil, or dust, it could mean the internal valve mechanisms are failing and need to be replaced.
Once you know the machine is clean and running optimally, check the software and sensor performance. While this type of basic monitoring is becoming more and more automated, it is still necessary for operators to keep a close eye on what’s happening in real-time. As an example, older models may still need to be manually calibrated, though new generations of color sorters eliminate this need by using internal calibration algorithms. Like any computer system, the sorter’s database and parameter settings need to be backed up on a regular basis.
Of course, the best way to maintain your color sorter is to hire a professional like Bratney. Our experienced and certified technicians can help you protect your valuable equipment and avoid unexpected shutdowns by conducting regular preventive maintenance.
Integrating color sorting machines into your processing operations can save you time and money while boosting your overall production and quality. For more information on improving the efficiency of your operations, browse our blog!