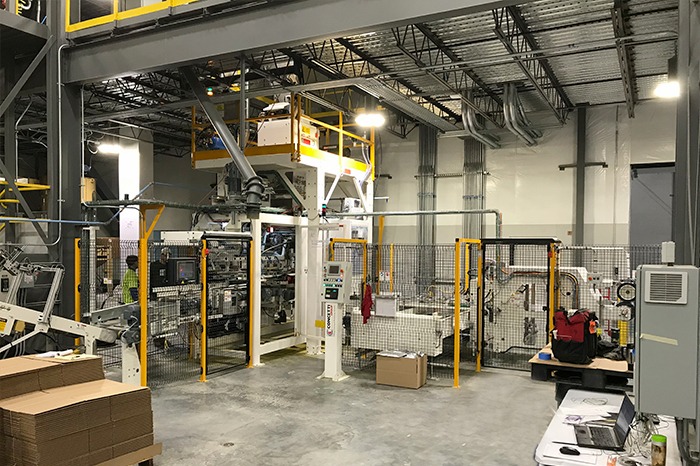
For more than a thousand years brewers have been using hops to give beer its characteristic bitterness and flavor. To the cognoscenti, hops and beer making are inseparable. The many varieties of hops, prepared and added in different quantities and at different times during the brewing process, have given rise to the huge range of different beers that we know and enjoy today.
Bringing hop growers and brewers together to further the interests of both in one of the largest hop growing areas of the U.S. is the aim of Mill 95, a brand-new hops processing plant located near Wilder, ID. Designed to meet the needs of the growing craft beer industry both locally and globally, the plant will feature two temperature-controlled storage facilities and a hops pelletizing plant. The facility also includes a specialized Concetti bag filling system to package the processed crop for transportation and use across the world. Concetti, based near Perugia in Italy, is a leading European manufacturer of bag filling and closing systems.
Fresh hops pack the most flavor and aroma but slowly degrade over time so storage conditions after harvesting and packaging methods are vitally important to protect the hops’ most important characteristics, as well as Idaho’s reputation for top-quality products.
The Concetti line is designed to work with heat-sealable PE-coated aluminum foil packs in 11-, 22-, and 44-lb sizes without micro perforations. Bags can be flat and pre-made with integral zipper or, alternatively, created from tubular reel stock. In this respect, Mill 95 will be able to offer users a choice of having a resealable pack to help preserve freshness after first opening, or a plain bag produced on the line from a continuous reel. Both pack types will have the benefit of modified atmosphere packaging (MAP) to blanket the product with inert nitrogen, preserving the flavor and aroma until use. Output is up to 1000 bags per hour on the smallest pack size.
Concetti has a long history of supplying versatile packaging lines that provide the user the maximum flexibility to fill a wide range of bag sizes and types but, more importantly, to do this with the minimum of downtime between changeovers. Switching from one pack size/type/weight to another is simply a matter of a program change with all physical adjustments, like sealing conveyor height and bag magazine backstop position, being made by servomotors under the control of the PLC. The weighing controller is also linked to the PLC by a network, so if necessary, the target weight and feedgate aperture are automatically adjusted at the same time. Changes are made in less than 90 seconds without any tools or spanner activity being required, making it ideal for short job runs, while avoiding operator set up errors.
All material contact surfaces are AISI 304 grade food-quality stainless steel. The interlocked access doors allow for inspection and cleaning of any residues between products. The Concetti line begins with a small feed hopper and net weigher with gravity feed gate. A brushless motor system drives the two-speed gate, providing for precise and programmable dosing control when handling the wide weighment range.
The Concetti IGF 1200 automatic filling and closing machine is fully enclosed behind transparent interlocked safety doors and is equipped with an inert gas MAP system at the bag holder. Bags are either premade with a resealable zipper at the bottom and delivered from a three-stack magazine, or cut from continuous tubular reel stock and welded at the bottom to form each bag. Before automatic pick-up and placing on the filling spout, each bag is accurately centered to ensure precise and consistent positioning. After filling, the opened bag mouth is immediately closed to retain the inert gas and, while still closed, transferred to a heat-sealing device, which produces a hermetically sealed pack, preserving the carefully processed and pelletized hops inside until required.
When filling premade bags, the operator can safely and continuously replenish the empty bag magazine without stopping the line. Using tubular reel stock allows long, unattended production runs, while providing a secure, high-quality pack at the lowest possible cost. About 7000 bags can be produced from a single reel without the operator needing to replenish the magazine. The reel feed system can handle printed film with a registration mark to determine the bag length or, if required, plain film can be used when a shaft encoder accurately calculates the required bag length. A motorized device is incorporated to lift the reels and make changing a quick, safe, and simple task.
Filled bags are laid flat by an overhead turner as they exit the machine on a short belt conveyor. The Concetti system is complete with dust extraction connection points and mesh guarding is provided with interlocked access doors or light barriers for operator safety.
An Allen Bradley Compact Logix PLC and graphic terminal operator interface controls the filling line, providing status and alarm message display, as well as permitting the creation and editing of stored parameters for each bagging program.
As with all Concetti systems, the Mill 95 filling and closing line was erected and tested in Italy before shipment, using product, bags, and reels provided by the client. The system was supplied by Concetti’s U.S. agent, Bratney Companies, and is supported in the U.S. by Concetti North America in Hoschton, GA, and Bratney Companies with offices in Des Moines, IA, and more locally to this project, Boise, ID. A teleservice system via the Internet, either by U.S.-based engineers or direct from the Concetti factory in Italy is also available.
Graham Rawlings is senior packaging expert, Concetti. For more information, visit www.concetti.com.