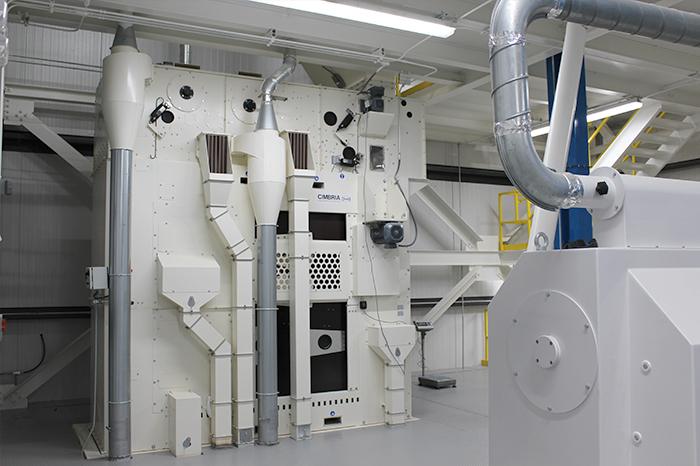
Grain cleaners are commonly divided into two categories, high-capacity grain cleaners and precision grain cleaners. Both types perform different functions in a processing plant and based on the needs of a plant and the grain or seed they condition, the cleaners may be used in conjunction with each other or used on their own. We take a closer look below at function, benefits, common applications, and some innovations we’ve found in challenging applications.
What is a High-Capacity Grain Cleaner?
A high-capacity grain cleaner, sometimes called a pre-cleaner, is a specialized piece of agricultural machinery that is used to clean large quantities of grain or seed. The machine typically consists of a series of perforated screens, sieves, and air blowers that work together to remove larger foreign material, debris, dust, and other contaminants from the grain allowing it to be stored safely, shipped more efficiently and to enhance its appearance and marketability. High-capacity grain cleaners are typically used in commercial and industrial applications, such as grain terminals, barge loading terminals, and grain elevators.
What is a Precision Grain Cleaner?
A precision cleaner is another type of grain or seed cleaner designed to remove smaller impurities and provide a high-quality finished product. Precision cleaners will remove a high percentage of foreign material, damaged grains and other impurities that allow grain to meet stringent export standards or to improve the downstream processes in a plant. Generally, the precision cleaners feature more screen decks that allow for a much more precise separation on size. They also should include aspiration air systems that include air volume and air velocity adjustments allowing plant operators to make precise separations on a wide range of grain and seeds. High-capacity, precision grain cleaners are typically used in export grain terminals, malt houses animal feed plants, food production plants, inland grain terminals and seed plants prior to the final cleaning process.
Why are Grain Cleaners Important?
The grain cleaning process is critical to the quality of your final grain, seed, feed or food product. It's important to remove as many contaminants as possible during the pre-cleaning stages that could otherwise damage downstream equipment, plug spouting, plug bin discharges, and cause contamination of finished products. Grain cleanliness also reduces the chances of insect infestations and mycotoxin contamination. Quality grain cleaning equipment is a basic standard for processing plants and terminals to remain competitive, but what aspects of your production should you expect to get better as you incorporate the technology?
Grain Cleaners Increase Your Production Lifespan
The first reason is to protect your investments and your productivity. Coarse contaminants like sand, sticks, and rocks will damage the equipment in your plant. Even with care and planned maintenance, this can lead to costly repairs, downtime, or even replacement. Even well-built equipment with parts designed for longevity can be heavily affected by the erosion effects of foreign materials at high quantities. A high-capacity grain cleaner is your solution for increasing the lifespan of all the downstream processing equipment and material handling equipment in your plant.
Grain Cleaners Reduce Your Invisible Threats
Impurities in your product go beyond foreign materials like rocks and sticks. Insects can make their way into harvested grain. Their presence in the equipment can create impurities that affect the future product as it moves through your process. One of the most important issues that can come from grain cleanliness is feed and food products contaminated with mycotoxins. Mycotoxins are poisonous compounds that can be found in grains that have been infested with mold. Infestations are more likely to occur in dirty grain, dust, small or broken fractions, as well as low-density and shriveled kernels. Although high-capacity cleaners can't do all the work, they play a necessary role in eliminating as much of this contaminated grain as possible.
Grain Cleaners Improve Your Bottom Line
Any business owner knows that one of the most important things to consider is the bottom line. How can you increase profits and decrease losses? One way to do this is to invest in a grain cleaner. The right grain cleaner will increase your yield while also improving the quality of your product. Very simply, selling more product at a higher price increases profit. In addition to the financial benefits of investing in a grain cleaner, you will also be able to build a reputation as a high-quality and reliable producer, which can lead to repeat business. Therefore, investing in a grain cleaner is a wise choice for any business owner who is looking to improve their bottom line.
Grain Cleaners Optimize Your Production Process
Grain cleaning is a critical part of the production process and investing in high-quality grain cleaning equipment is essential for any feed or grain facility. Grain cleaning removes contaminants from the grain, protecting your equipment and improving the quality of your product. Grain cleaning also helps to improve your bottom line by increasing the efficiency of your operation and reducing the amount of waste you produce. Whether you're looking for a simple way to improve the quality of your product or looking to invest in high-capacity grain cleaning equipment, grain cleaning is an essential process for any feed and grain facility.
What are Some of the more Difficult Cleaning Applications?
Cleaning Malt Barley
Cleaning barley for malting requires a high degree of accuracy to remove foreign materials, but also damaged, diseased and thin kernels. Having a clean and consistent product is critical to maximizing the efficiencies in the malting process to produce a premium malt.
Cimbria barley cleaners are typically of two types. The Combi series or the Mega series and use of either depends on the capacity requirements of your specific application. In either case, both machines feature precision feeders that allow for highly accurate aspiration systems to perform quality separations. Working in conjunction with the aspiration systems, the screen layouts and patterns match the proper screen surface area and optimal product retention time for maximum screening efficiency.
Another advantage of Cimbria cleaners for malt barley cleaning is gentle handling. Damaged kernels will not germinate as intended, creating losses or “plant shrink” that reduce the efficiency of a malting operation.
After the malting and kilning process, Cimbria Combi or Mega cleaners are often used to clean the fresh malt. Their aspiration systems remove detached husks, culms and light chaff. Screens can be used to remove any large clumps that may be present and to sift any remaining fine or thin material out of good malt.
At loadout, Cimbria cleaners provide one final opportunity to remove light and fine material that was generated by material handling equipment or during storage.
Matching Quality with Capacity at Export Wheat Terminals
Historically, the grain ran through inland and export grain terminals was cleaned through rotary screeners and then through a large bank of indented cylinders. Aspirators were used to provide some means to remove fines and dust but these systems lacked the accuracy required to provide a high-quality finished product.
Pushed by changing market conditions that required higher standards for exported products as well as increased cleaning capacity Bratney recognized the opportunity to improve this process. Through testing in our lab we identified a more effective flow that could be installed into a much smaller space. From that testing, we worked with Cimbria to develop a high-capacity cleaner that would meet the increased capacities that the large grain terminals required to be competitive while delivering a cleaning quality that traditional methods could not produce.
The real innovation in this new approach was combining a cleaner capable of 10,000 bushels per hour with length separation and this concept quickly proved its worth. This innovation through the collective efforts of Bratney and our proprietary equipment partner, Cimbria reduced the number of indented cylinder separators needed in a grain terminal from 50 or more down to 2 saving terminals huge amounts of money in equipment, electricity, maintenance, and floor space.
Cleaning Millet
While millet is probably best known as the main ingredient in bird food, it has more recently become well known as a healthy grain for human consumption as well. With its growing popularity in human foods, we’ve seen an increase in product purity standards in the millet industry. We’ve been very successful meeting 99+% purity requirements on millet for human consumption with a mix of the correct screen flows and precision air systems available on Cimbria cleaners.
If the overall goal for your facility is to have better grain quality at a faster rate, Bratney can help. No matter what your grain cleaning requirements are, there is a pre-cleaner or precision cleaner that will meet your needs. Contact us today to learn more about our products and our tailored design services.