Reduce Product Damage and Ensure Consistency with Robotic Palletizing
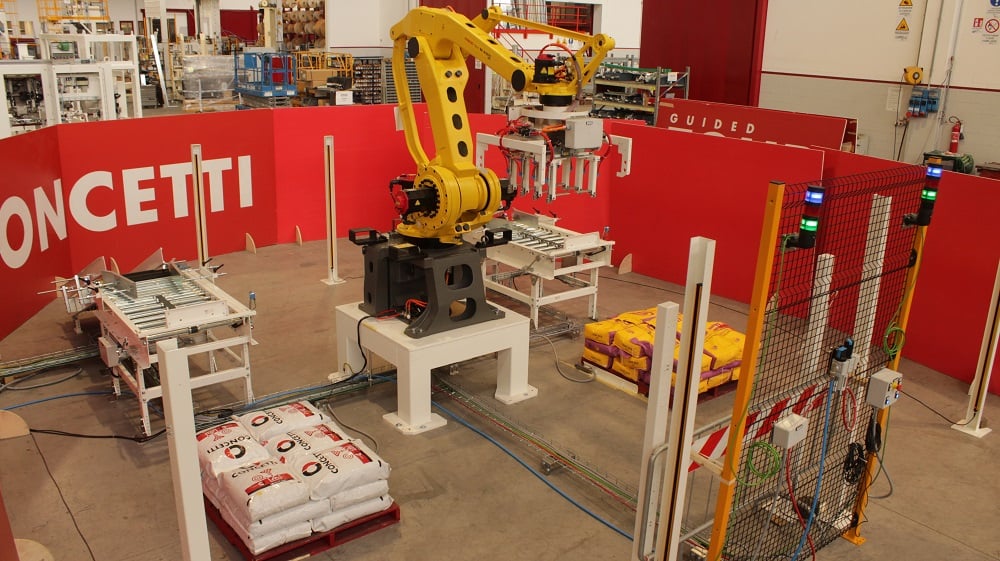
Both small and large operations are seeking innovative ways to increase efficiency and decrease downtime. Automatic palletizing is a proven solution for optimizing productivity, minimizing downtime, and reducing errors in shipping and storage fulfillment. Warehouses today face staffing shortages due to high turnover rates and labor disruptions. As a result, warehouse owners and managers are looking to robotics and automation for solutions. Implementing pallet automation helps warehouse managers redistribute their labor forces to focus on essential tasks while resting on the efficiency of an accurate, safe automated palletizing system.
Palletizing Basics
The process of stacking large quantities of bags or boxes onto pallets for shipping is referred to as palletizing. Originally, palletizing was a manual task. Today, warehouses can use palletizing machines.
Typically, items are stacked according to weight in a formation that maximizes stability and helps maintain product integrity in transit. Pallet stability is an expression of the stack’s ability to remain upright when subjected to the forces experienced during dynamic events, such as accelerating, braking, and cornering when in the back of a truck or on the tines of a forklift.
Automated Palletizing
Automated palletizing uses machines to stack packaging containers into a single unit for transport using either a conventional set-up or a robotic one. A floor-level conventional palletizer pushes boxes or containers into rows to align them against a stopping point. When the rows are completed, they are then moved to a layering table that drops them onto a pallet. High-level conventional palletizers utilize pallet movement instead of a layering table to build layers.
Robotic palletizers are computer-operated machines that can perform tasks with minimal need for human interaction. They use an arm to grab items from a conveyor to form layers and create a unitized load. One significant difference between conventional and robotic palletizers is that the robotic versions can work on multiple SKU types and pallet designs, while conventional types are often limited to one specific pallet design.
Benefits of Automated Palletizing
Robotic palletizers offer many short and long-term benefits, providing a more efficient way to assemble unitized loads while protecting products and employees. Palletizing robots are versatile and can operate in many environments, including warehouses or manufacturing plants. Their size and design make them appropriate for use in locations with either high or low ceilings, allowing you to optimize use of your warehouse space.
Increased Efficiency and Productivity
Industrial automation improves efficiency and accuracy in the pelletizing process, allowing you to reduce waste, save money, and better satisfy your customers.
Reduced Labor Costs
Automatic palletizers do the repetitive heavy lifting that you would otherwise have to employ manual laborers to perform. Plants and warehouses can reduce staffing or repurpose workers, reassigning employees to more important tasks that machines cannot handle.
Improved Safety
Many common workplace injuries result from repetitive motion or lifting. Reducing the need for manual stacking and lifting protects employees and companies by reducing the risk of physical injuries.
Minimized Damage
Manual palletizing processes involve many risks. Incorrectly placed boxes can compromise load stability, which can result in damage to products or harm to workers. Robotic palletizers provide consistency and stability, reducing the risk of product damage or employee injury due to dropped or inappropriately stacked items.
Industries That Benefit from Palletizing Automation
Pallet automation is essential for companies to keep up with demand. Many industries benefit from automated palletizing, including food and beverage, pharmaceutical, retail, automotive, agriculture processing, and many more. Automation can streamline shipping efforts, increasing distribution speed and efficiency.
Warehouse automation improves efficiency and food safety, helping the agriculture industry transition food from farm to warehouse to table. One crucial aspect of food safety is expiration dates. Ensuring rotation based on first expired, first out can be challenging in large conventional warehouses with manual methods of operation. Palletizing automation solutions and using robotic automation for storage, retrieval, and packing alleviate these challenges, reducing risk to consumers while increasing efficiency and productivity in agricultural processing and conditioning.
Integrating Automation
Warehouse automation benefits both small and large-scale operations. Successful automation integration is a detailed process that’s best undertaken after thoroughly assessing the site’s logistics. A detailed account of location, size, skill sets, and workflow processes is imperative. Once a plan is in place for automation integration, employee training is critical. Automation equipment will require ongoing maintenance and service and staff members who are familiar with automation processes and workflows. Bratney can help you get started with equipment installation and training.
Bratney
Bratney has generations of experience in agriculture systems and equipment. Through the years, technology has made huge advancements, and we have adapted by keeping up with new automation technology to help the agriculture industry enhance productivity safely and securely. We pride ourselves on delivering the best equipment, engineering, and product solutions to our customers in the agricultural sector. With innovative process design and engineering expertise, we are ready to help you integrate automation into your warehouse workflow. We offer an excellent selection of palletizing machinery with various systems that work for large or small warehouse operations.