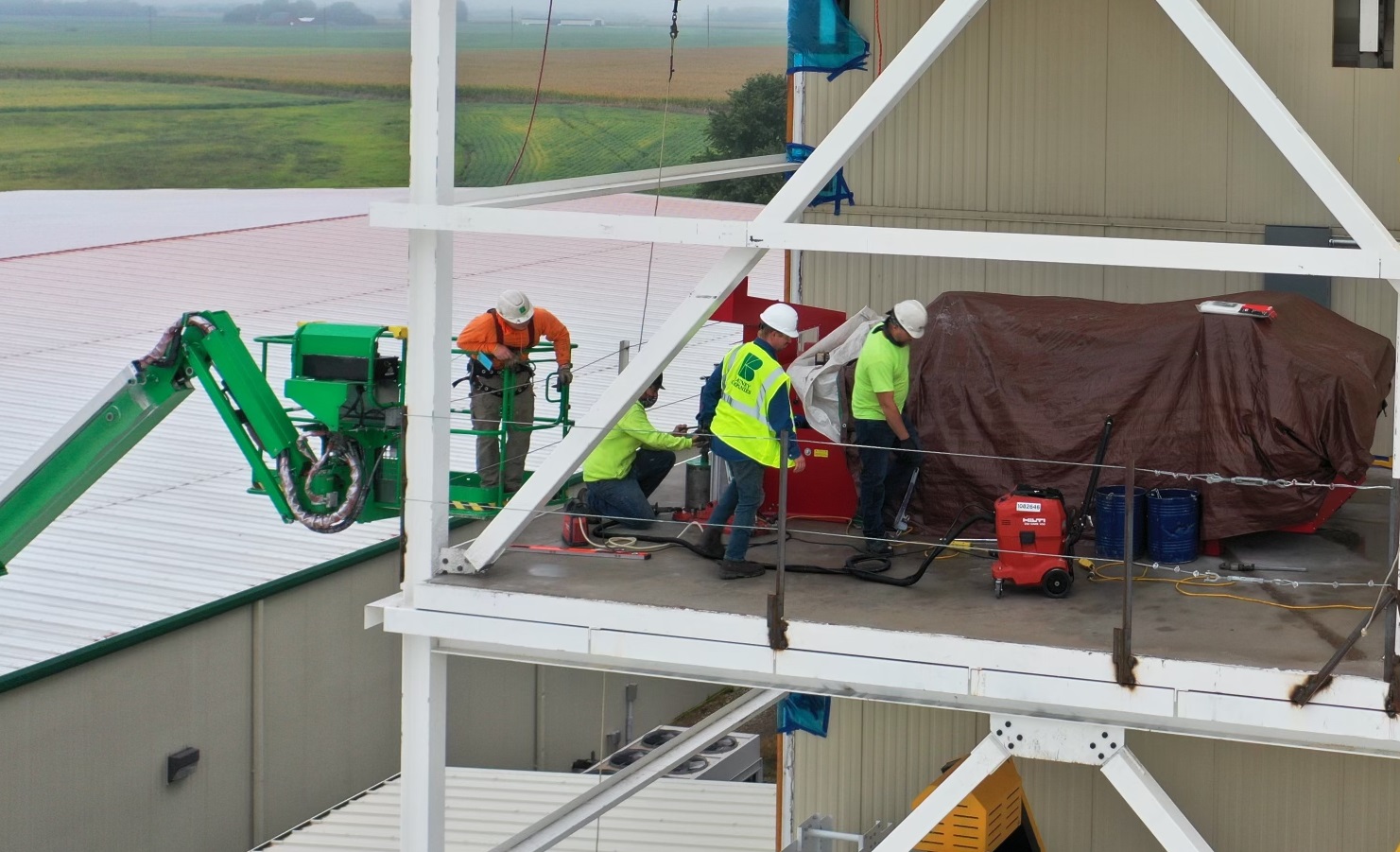
Worker safety is one of the most critical considerations in building the most efficient industrial process designs. Most construction businesses place a high value on it. Workers must be protected by providing correct training, suitable safety equipment, and industrial machinery intended to lessen the possibility of accidents. An in-depth understanding of these aspects allows you to see the big picture and transform your concept into a real, practical project.
5 Key Components of the Industrial Construction Process and Design
A seamless construction process is dependent on numerous crucial factors, including:
1. Project Conceptualization, Design, and Planning
Project conceptualization is where a project's initial concepts are considered before beginning a comprehensive design phase. Conceptualization normally comes after locating the project's site and specifying the relevant building codes. It's essential to involve an architect at this point to make sure everything is viable.
2. Securing all the Required Building Permits
It is vital to get the relevant building licenses before beginning the construction due to the fact that various specialties require distinct permits. The process can take a while since numerous conflicting agencies must approve the project.
3. Getting to a Pre-Construction Phase
This phase encompasses all the work done on the project prior to the actual construction. It only takes place after the design is simplified, the resources are gathered, and the project planning is completed.
4. The Procurement Stage
During the procurement phase, the project team acquires the necessary resources. The difficulty of this stage is determined by the scope of the project, the anticipated start date, and the resources that are available. At this point, the general contractor gives the subcontractors smaller tenders. New construction takeoffs from the building blueprints are typically the first step in the process and are used by the subcontractors to procure labor, supplies, and the scope of the project.
5. Finally, the Construction Phase
The construction phase is when a construction crew begins digging, and a blank field evolves into an imposing building.
How Does Worker Safety Influence Industrial Process Design?
Construction is a dangerous profession, with a significant chance of on-site accidents as well as more complicated dangers that must be taken into account when working off-site. That's why worker safety is one of the most critical considerations in building the most efficient industrial process designs.
Does OSHA Affect the Industrial Process and Design?
Osha influences how industrial processes are designed. The Occupational Safety and Health Act says that companies must follow safety and health rules set by OSHA or by a state with a federal program that OSHA has approved. Section 5 (a) (1) of the Act, also known as the "General Duty Clause," states that employers must give their workers a workplace that is free of known dangers that could lead to loss of life or serious bodily injury.
Where Can You Find the Guidelines?
The United States Department of Labor provides construction companies with guidance and tips on maintaining a healthy and safe workplace. The department also offers suggestions that are both advisory and educational in nature, as well as summaries of the laws and regulations that govern health and safety.
Standards for Maintenance of Equipment
Regular maintenance is required to keep equipment, machinery, and the workplace safe and dependable. Poor or no maintenance can result in unsafe circumstances, fatalities, and health issues.
The following OSHA requirements are specific to equipment maintenance:
- To avoid workplace injuries, machines with broken or missing safety features should be taken out of operation.
- Emergency shutdown procedures must be used if safety precautions need to be disabled in order to repair equipment or perform normal maintenance.
- All power sources must be cut off and shut out before any work may commence in the event of electrical risks or operating machine parts.
What are the Dust or debris regulations?
Explosive Dust Control in the Workplace
Combustible particle dust can burst into the air under the correct conditions. Explosions of this nature can cause serious injury, death, and property damage.
Combustible dust risks are under OSHA's National Emphasis Program (NEP), which focuses on U.S. hazards. Even though OSHA can't penalize your company for flammable dust, it can utilize other regulations to enforce worker safety.
Additionally, OSHA currently has regulations for respirable crystalline silica in the construction industry as well as marine and general industrial. Companies using alternative exposure control techniques need to:
- Ensure that workers are not exposed to more than 50 micrograms of airborne asbestos per cubic meter of air in an eight-hour workday.
- Use engineering and work practice controls, like dust collection systems, to reduce workers' exposure to the PEL.
- Keep track of how much inhalable crystalline silica workers are exposed to.
Planning and Implementing Worker Safety Strategies
How do you plan for a safe working environment?
Designing a safety plan requires advance preparation, but once completed, your team will be prepared for any incident. Following a step-by-step guide can help you complete your safety plan more efficiently and with greater accuracy.
Here are some common safety plan components:
- Objectives and policy declaration.
- List everyone to be held accountable.
- Detailed instructions on how to obtain help in case of an emergency.
- An account of the present condition and location of the site
- Identification of potentially dangerous conditions.
- Control of potential hazards and precautions to prevent injury.
Worker Safety Intervention Strategies to Build into Your Business
You can reduce workplace accidents by using safe work procedures and practices as well as providing a secure environment with appropriate tools and resources.
Here are four worker safety intervention strategies that can be built into your business:
- Informational and educational interventions may decrease injuries by instilling new understanding and skills in safer work conditions.
- Compulsory and persuasive interventions can prevent injuries by influencing workers' and leadership's attitudes toward using safer working practices and implementing safe working conditions.
- Facilitative interventions might decrease injuries through supportive actions such as the use of safe materials, equipment, and building design.
- Multifaceted interventions may prevent injury by combining the aforementioned strategies.
What are the Benefits of Improving Worker Safety?
Improves Employee Retention: When workers see their employer taking precautions to keep them safe from workplace risks, they feel more appreciated and safe in their job.
Increased Productivity: Having fewer accidents, reduced downtime, and greater morale can contribute to increased efficiency.
Reduced Company Liability: If a worker is hurt on the job, your organization may be held liable by the injured party, their union, or the federal government.
Take Action to Safeguard Your Workplace
Working with a business that accounts for industrial process safety and productivity on the front end will save you a lot of headache while assuring seamless process design. Visit Bratney Companies for expert assistance with all of your industrial building needs.