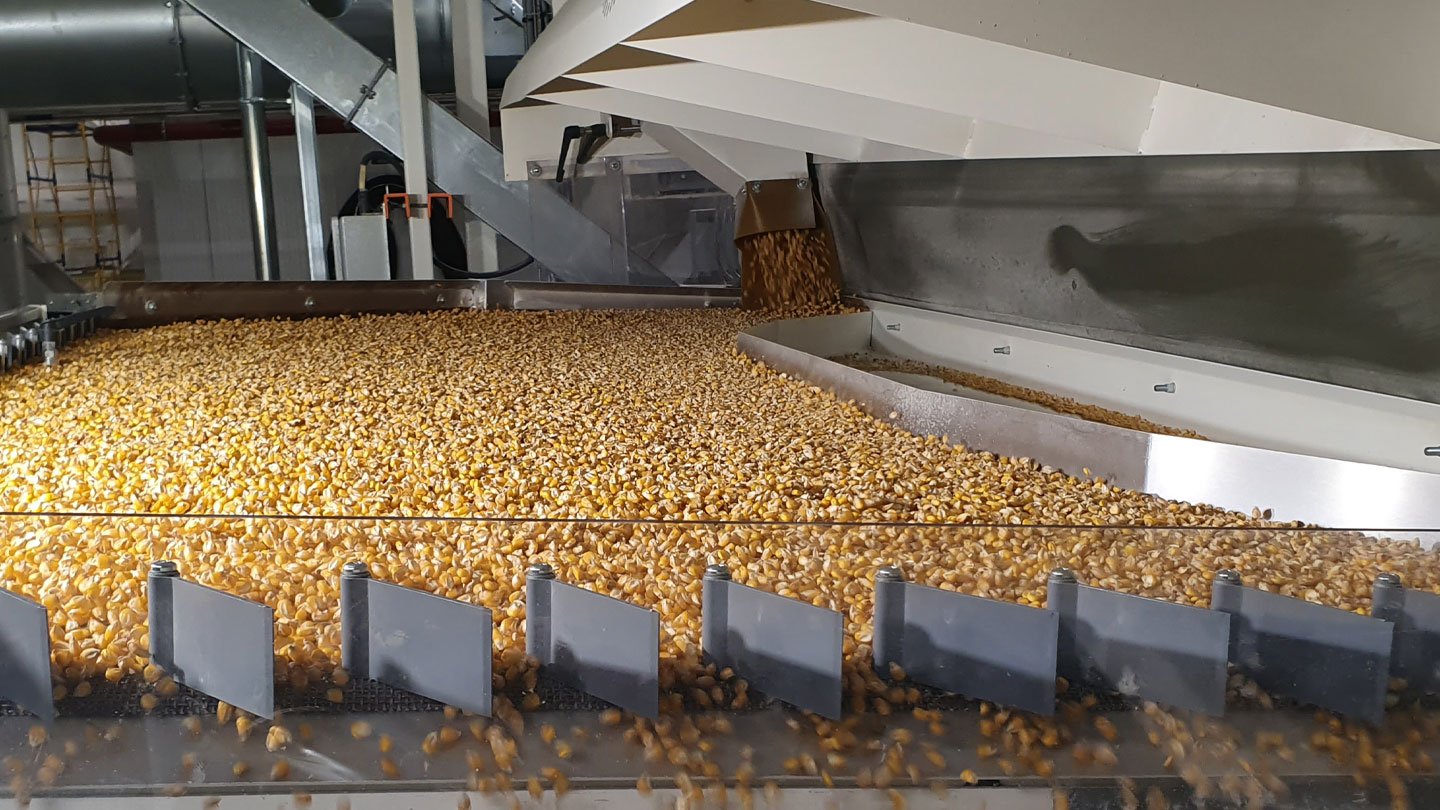
Gravity separators are vital tools in various industries, from agriculture to mineral processing, where product quality and precision are essential for success. These sophisticated machines remove impurities by separating materials with similar shapes and colors based on density differences, making sure only the highest quality products pass through the process. Choosing the right gravity separator for your facility is crucial to enhancing overall product quality and separation accuracy.
Understanding the Principles of Gravity Separation
Gravity separation relies on the “fluid bed” principle, which is what allows gravity separators to achieve such high levels of precision. Essentially, the product is separated into layers based on specific weights. Materials are suspended in a stream of air, which is blown upward through a wired mesh or textile cloth deck. The materials are directed to the deck, and as the air continues to flow upward, it causes the material to become suspended - or “fluidized.”
Then, the heavier particles sink to the bottom of the deck, while the lighter particles rise to the top. Over time, this creates layers of the material with the most dense on bottom and the least dense on top. Then, the gravity separator will use vibration or tilting to move those layers to different collection points. This technique is especially effective for materials that are similar in shape and size but differ in density. As an example, in seed processing, this process can separate the fully developed seeds from the immature or damaged seeds, even if they look to be similarly sized.
Since this method relies on density differences, it can help better distinguish between particles that other sorting methods, like air screening or color courting, might not handle quite as effectively.
Key Features to Consider
When choosing a gravity separator for your facility, there are a few things to keep in mind to ensure you select the most appropriate and efficient machine for your needs - now and in the future.
Feeding Devices
A consistent and controlled feed is incredibly important for optimal separation. Look for feeding devices that can provide a steady flow of material to the deck without overloading. This ensures a more accurate separation and enhanced efficiency.
Dust Hood Options
Dust management is essential for maintaining air quality and preventing loss of product. The right dust hood can improve the working environment and efficiency. Gravity separators can offer both partial or full dust hood options. Partial dust hoods are ideal for less dusty materials, like EXAMPLE, while full hoods are best for materials like EXAMPLE, where dust control is critical.
Deck Materials and Design
The deck is the heart of the gravity separator, and the design can greatly influence performance. When you’re choosing the right machine for your facility, pay attention to gravity separators that have square mesh designs. This type allows for quicker separation and lets the heavier materials discharge faster. This allows the remainder of the desk to process even more material effectively.
Ease of Operation
As innovative and tech-friendly as facilities have become, at the end of the day, it is a person controlling the machine. User-friendly controls and adjustable settings are crucial for efficient operation. Look for separators that allow operators to quickly adapt to different materials or separation requirements. The ability to fine-tune parameters like air flow, deck angle, or vibration intensity can make all the difference in accuracy and overall productivity.
Stratification Pins
Stratification pins are small, vertical pins on the deck surface that help create turbulence in the material bed, promoting better stratification of particles based on density. Consider the design and arrangement of these pins to significantly improve separation efficiency. They are particularly useful for those materials with subtle density differences.
Stone Traps
A final consideration when choosing a gravity separator are stone straps. These are an incredibly important feature, especially in agricultural processing. Much like their name suggests, stone traps capture and remove stones or metal pieces before they can damage the separator or contaminate the final product. When choosing a gravity separator, assess the effectiveness of the stone trap system to make sure it can protect your equipment and maintain the highest levels of product purity.
These features enhance the separation process by preventing contamination and ensuring that only the desired materials are processed.
Benefits of Using Gravity Separators
Investing in gravity separators for your facility offers several key advantages. This additional piece of equipment can elevate the quality of your product by accurately separating pre-cleaned materials. Gravity separators can achieve a much higher level of precision that is difficult for other methods to match, like air screen cleaning or color sorting alone.
These machines are also very versatile, managing a wide range of materials for invaluable use in diverse industries. From seed cleaning to removing damaged products, to improving the quality of wheat, and more, you can find applications in any industry.
Common Applications and Materials
Gravity separators are used for specific separation tasks, including removing damaged cereals, separating cocoa beans from germs, or detecting insect damage in dry edible beans. This is critical for maintaining product quality and meeting industry standards.
These machines can be used for a wide variety of materials: corn, cocoa beans, coffee nuts, dry edible beans, and seeds. However, it is important to remember that pre-cleaning these materials before they enter the gravity separator is crucial. This helps remove a large amount of debris to ensure the separator functions at its peak efficiency.
Factors Affecting Performance
Several factors can influence the performance of your gravity separator. To maximize its effectiveness, consider the following:
- Deck Covering: The right deck covering, including the material and texture, can affect how well the materials stratify and separate. It's essential to choose one that matches your specific material needs.
- Air Quality and Dust Management: Maintaining good air quality and managing dust are critical for maintaining the efficiency and longevity of the separator, as well as the health and safety of its operator.
- Regular Maintenance and Cleaning: Keeping your machine well-maintained and clean helps it continue to function effectively and prevent any buildup of materials that could hinder performance.
Customization Options
Gravity separators can be customized with various assembly variations and add-ons to meet the specific needs of your facility. This customization ensures the separator can handle a wide range of materials and tasks, maximizing its versatility and efficiency.
For instance, you can customize your gravity separator for a specific material, or add discharge spouts for sorting into several grade categories. The feeding system itself can be customized depending on your needs: vibratory feeders for consistent material flow, belt feeders for delicate products, or valve feeders for precise handling. You can also customize the air system with high-pressure air, zoned air control, or automated air flow. There are also options for automation and controls, like touchscreen interfaces with preset programs for different materials, remote monitoring and control capabilities, and even integration with plant-wide control systems.
There are several ways to customize a gravity separator, and not all are listed here. Speaking with a professional can help you determine which features would be most beneficial for your particular facility and needs.
Importance of Proper Installation and Support
With most machines, proper installation is absolutely crucial for maximizing the performance of your gravity separator. Features like a counterbalanced eccentric drive can reduce vibration and wear, extending the machine's lifespan.
Expert installation and ongoing support are invaluable for ensuring that your machine operates smoothly and continues to meet your facility's needs. Make sure to meet with a professional for support with this process from beginning to end.
Choosing the Right Gravity Separator
Choosing the right gravity separator is a critical decision that can significantly impact your facility's product quality and operational efficiency.
By considering key features, understanding the benefits, and ensuring proper installation and maintenance, you can optimize your separation process and ensure that your products meet the highest standards.