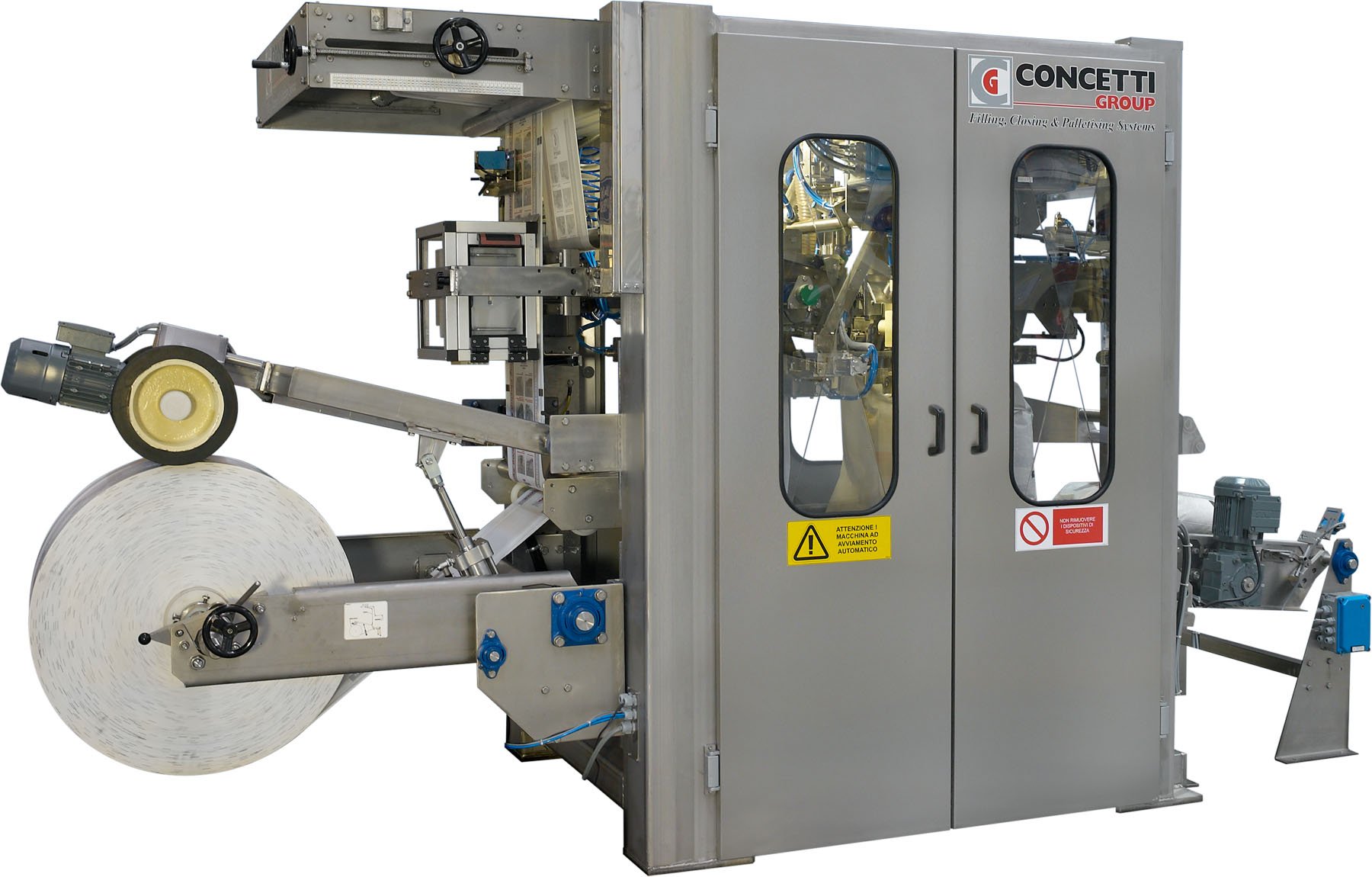
If you’re looking for a machine for filling bulk products up to 100lb into open mouth plastic, low-density polyethylene (LDPE) bags, today’s tubular form fill and seal (FFS) systems may offer some distinct advantages. This article looks at some of the reasons why tubular FFS technology is fast becoming almost the defacto standard in many industries, replacing both vertical (VFFS) and conventional systems for pre-made plastic and perhaps surprisingly, even paper bags.
Installing an automated bag-filling line for packaging loose bulk products up to 100lb capacity can be an expensive business even if you get the investment right. But get it wrong and the right solution can begin to look like a bargain. There is a bewildering array of different suppliers and machines available to choose from but if you need to fill open mouth plastic low density polyethylene (LDPE) bags you might want to narrow it down to a tubular form fill and seal system. Tubular form fill seal (FFS) technology continues to gain market share compared with both vertical FFS (VFFS) and conventional systems where pre-made bags are placed, filled and sealed by separate, discrete devices, sometimes even made by different manufacturers.
In more recent years developments both in machine technology and film construction has succeeded in converting industries where multi-wall paper bags, valve or open mouth, have been the traditional and preferred method, to the benefits of LDPE packaging. So what exactly is the appeal of the tubular FFS solution to bag filling?
FFS Systems: Vertical Versus Tubular
Form fill seal machines are the integrated solution with everything done in one compact system. The bag is cut and formed from a continuous reel, then filled and sealed before emerging as a finished pack. With a few exceptions, FFS machines fall into two generic types, the vertical or VFFS, using single wound film passing vertically through the machine from top to bottom. This is the original concept, owing its beginnings to the need for small, high-speed retail packaging. VFFS suppliers are often most familiar with this retail market sector but some also offer machines for larger industrial sized packs. Because the VFFS uses a single wound sheet of film, to make the bag, in addition to top and bottom seals, a longitudinal or side-seam is first needed to construct a tube and if gussets are required these are formed inside the machine.
Tubular machines, a type of horizontal FFS system, are a later development aimed in general at larger pack sizes and more rugged industrial applications where they offer significant advantages including higher speeds. The key difference being the use of tubular film, manufactured with or without gussets, so there is no longitudinal side-seam to make and operations move horizontally through the machine where forming, filling and sealing take place simultaneously on different bags. Other variations of FFS system are available but tubular almost certainly has the benefit of using the minimum amount of film and needing the minimum amount of machine based film-sealing. For dusty products this can be a real advantage.
Both tubular and VFFS machines tend to be have smaller footprints than lines with separate bag placer and sealer, an important factor where space is limited.
Costs
Capital costs vary considerably depending on supplier so it’s difficult to give hard and fast rules but it is worth remembering a PE bag-filling line can easily consume in one year film equivalent to the line’s purchase price. So, for a machine with an expected 20-year life or more, the initial price can represent less than 5% of the total cost of ownership. Film costs over the system’s life will have a much greater impact on the investment than the machine itself.
All FFS machines use film purchased on a reel. Each reel, depending on film thickness, bag length, and whether it is single wound sheet for VFFS or flat or gusseted tubular film for tubular machines, will contain perhaps 2000-6000 typical 50-lb bags. In contrast to pre-made bags, there is no welding or stacking at the manufacturer and since the film is usually blown as a continuous tube in any case, after printing it is only necessary to wind the tubular reel onto a cardboard core. Single-wound film starts as a tube but is simply slit before being wound as single sheets. Reels should therefore always be cheaper to purchase than pre-made PE bags.
For any given bag size, the tubular reels of a tubular FFS machine will need less film compared to the single wound film of a VFFS system because the latter requires an overlap of perhaps 1 in. or more in order to create the longitudinal seam and this adds a small percentage (perhaps 3% depending on bag widths) to the annual film costs. Over a machine’s life the small amount of extra film needed might equal more than half the initial investment, so not an insignificant sum.
All bag-filling systems must provide some ullage or space above the top of the product after filling to allow the closing seal to be made. Because FFS systems usually have more precise film handling it is often found less ullage is needed to produce a reliable seal so the bag itself can be slightly shorter, again contributing to important film savings throughout the life of the machine as well as giving the finished pack a better shape for subsequent palletizing. There is no need for any bag top trimming, further reducing film costs and waste.
Recent advances in film and machine development have added an extra weatherproofing dimension that allows external storage of, for example, cementitious or anhydrous products, and this cuts costs in the distribution channels by eliminating the need for covered storage and warehousing as well as actually extending product shelf life.
Users of paper bags, either open mouth or valve type, in these industries who find they are able to switch to PE would also expect to see dramatic savings in consumable costs. And Europe has tough recycling regulations: While both plain paper or plastic bags can be recycled, paper bags with an inner PE coating or liner commonly used to provide a moisture barrier, are not easily recyclable and can incur further costs for the customer if sent to landfill. It’s also bad for the environment.
Flexibility
For many users, some flexibility in being able to produce different pack sizes is a crucial consideration and both vertical and tubular FFS machine suppliers will usually offer a range, albeit not unlimited, of film widths and lengths in a single machine. Users with a wide product range and short job runs will be more interested in the changeover time between different pack sizes and here the tubular machine would offer advantages.
VFFS machines have a precisely made forming shoulder and tube over which the single wound film runs. Each VFFS bag width requires a dedicated shoulder and tube. Changing from one film width to another requires significant downtime while these large and sometimes heavy parts are changed. Tubular FFS machines can usually handle variations in film width without any change parts and will accommodate flat or gusseted tubular film, allowing an even wider range of bag sizes. Changeovers, excluding film reel exchange, can be made in less than 90 seconds under simple program control giving tubular FFS machines a much quicker turn round, and hence higher productivity, in day-to-day operations when producing several different pack sizes.
Reliability
In FFS technology the film is unwound from the reel and gripped securely at every stage throughout the entire machine cycle. Its position is always constant leading to fewer misfires, increased reliability, and better productivity. A pre-made bag placer relies on the operator stacking bags consistently with many older systems, allowing an uncontrolled or semi-controlled release of the filled bag, with the subsequent handling system having to relocate it before finally closing the pack. Not only does this lack of precision detract sometimes from the bag’s finished appeal, it also increases the risk of seal failure, spillage, and subsequent stoppages of the line.
Vertical or VFFS systems have to make the longitudinal side-seam on the machine in order to create a tube. This point becomes extremely important when handling a dusty material or powders where contamination of the seam increases the risk of subsequent failure. Tubular FFS completely avoids any possible failure in the longest seam by using seamless tubular film. The need for sealer maintenance is also correspondingly reduced.
A reel contains far more bags than a pre-made bag magazine and this eliminates the need to constantly replenish the stack, freeing the operator to carry out other tasks while being confident in leaving the line unattended. Reel changes are a matter of a few minutes work with many FFS machines incorporating integrated lift systems to make the operator’s task easier and safer.
Forming
Bag forming on VFFS machines is by simultaneously cutting the film and welding both the top of the filled bag and the bottom of the next bag using one assembly in a single combined action. Tubular machines have completely separate top and bottom sealing stations with the filling spout in between and bags being moved horizontally from one position to the next. Although more complicated crucially this gives access to the seal area allowing it to be cleaned prior to final sealing. In addition, the arrangement allows gross weighing to be fitted as an option and various deaeration techniques can be incorporated, including by a sintered plastic or steel vacuum probe being inserted directly into the bag. Additional stations can be added to give product-settling vibration, extra seal cooling, or to punch a carrying handle into the bag top.
Bag length is determined either by a photocell and printed registration mark on the film or by a machine mounted encoder if using plain, unprinted film.
Seal Cleaning
Heat and compression are used to melt the LDPE, weld the seal together and close the bag. On high-speed machines forced air or chilled water cooling is needed for the seal to be made sufficiently stable in good time to receive the product without failure. The bottom seal is made on fresh film right off the reel so reliability here is excellent. The same applies also to the top seal when packing dust free granular products. However, contamination of the top seal area when handling fine powders and other dusty products is inevitable and unless this is overcome, top seal reliability will be severely compromised. Seal cleaning is difficult on vertical FFS systems because the bag top is not accessible during sealing and these machines tend to rely on dust extraction methods alone. Tubular FFS machines on the other hand can be equipped with forced cleaning of the seal area, usually by a compressed air-jet wash, after the top is closed but just prior to sealing.
Cleaning demonstrably improves seal reliability and for extra security, some machines even offer a double seal at the bag top.
Advances in Film Technology
Anyone familiar with PE bags will appreciate that during filling some air is inevitably entrained with the product and after sealing, the bag is effectively transformed into a potential balloon. Palletizing becomes difficult and even dangerous if this air is not allowed to escape. For many products, PE pellets and the like, this is usually a simple matter of perforating or micro-perforating the film, something easily done on the machine or by the film supplier.
However, perforating the film to allow air to escape also allows moisture in. More than this, higher packing speeds means larger perforations so exacerbating the problem. For anhydrous and moisture sensitive products PE film was therefore unable to exploit it’s natural waterproofing quality and so had no real advantage over, for example, multi-wall paper bags with inner liners.
However, recent advances in both film and machine technology has led to a wider use of tubular FFS systems especially in applications where moisture proofing is a key requirement. Firstly, the use of special tubular PE film, often patented, with various types of micro-perforations incorporated into a factory made labyrinth seam. The labyrinth has a technical treatment internally to prevent it being sealed when the bag is closed. This allows air to be released slowly after filling but without permitting moisture to enter giving a weatherproof pack. The tubular FFS machines still requires careful design to remove as much air as possible prior to sealing otherwise palletizing immediately after filling may still prove difficult if not impossible.
Other developments have covered more improved techniques to create a partial vacuum in the pack before sealing that allows some tubular FFS systems to use plain PE film without any micro-perforations giving a totally hermetic seal, and at the same time, a highly compact bag offering the ultimate in waterproofing protection at the lowest film cost and with only a marginal reduction in output. These systems are already operating in the field allowing users to avoid the need for covered warehousing while still protecting the product and even extending shelf life. As well as offering better weather proofing the sealed bag is also cleaner when subsequently handled by distributors and users, notably so when compared to older unsealed valve bags.
Accessories and Variants
The integrated nature of FFS systems gives plenty of opportunity to build in options and accessories to suit a wide range of different applications. These are usually standard customizable options or specially engineered into the package by the manufacturer and tested thoroughly before dispatch.
If you sell into a retail environment you might want to incorporate handles into the bag or have a resealable zip closure. Printing a date or some identifying production data is easily done. Product is usually dispensed by weight using a separate net or even a multi-head weigher discharging by gravity but some sticky products like sugar with high levels of molasses for example, might be better being fed directly into the bag, in which case an integrated gross weigher can be provided inside a tubular FFS. Or a product might require deaeration probes to help a fine powder to settle, again easily incorporated into a tubular machine. Both of these options are clear advantages over the VFFS system.
So, given the reduced consumable and other costs, the increased reliability and flexibility of the tubular FFS, coupled with higher productivity and a better looking pack that is easier to palletize, perhaps we shouldn’t be surprised that these systems are not only growing in popularity but even succeeding in converting paper bag users to the benefits of PE film.
Bratney Companies is the exclusive supplier for Concetti in North American agricultural markets. Concetti is a manufacturer of turn-key automated packaging lines for bulk materials.