Filling the Labor Gap: Overcoming Skilled Labor Shortages in the Food Industry
Written by: Bratney
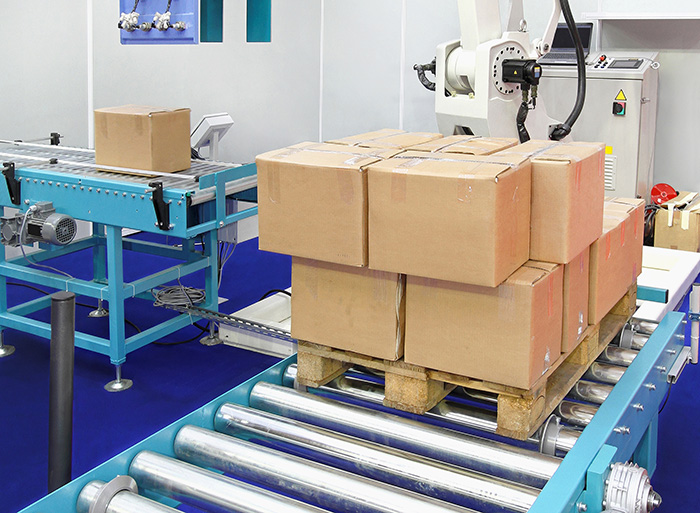
The food industry is not untouched by the current global labor shortages, and has actually been experiencing a general decline for several years. Food processing facilities, specifically, are struggling to find enough skilled workers to staff their operations. This shortage of qualified employees poses a major challenge in maintaining high standards of quality and safety.
Meeting demand in the food industry requires skilled workers to safely handle, prepare, and package the products. The growing gap in labor puts pressure on maintaining high food safety standards while simultaneously putting more strain on employees that already have less bandwidth to consistently follow proper protocols.
So, here’s the question those in the food industry are asking themselves: how can facilities keep up with demand in the midst of labor shortages, while not sacrificing safety and quality?
Higher Pay is Not Enough
Offering higher wages may attract some skilled workers in the short term, but this is not a sustainable, long-term solution for retaining talented staff. There is simply no guarantee that employees will stick around without feeling invested in and cared for by their employer — regardless of position or industry. Hiring temporary employees can also be a short-term solution, but these candidates are rarely suited for leadership positions, which adds to the challenges currently facing processing facilities.
Food processing facilities need reliable access to employees who thoroughly understand safe food handling procedures and other protocols, as well as those who possess the knowledge to properly operate specialized machinery. When those key positions are left unfilled, it introduces significant risks of contamination or workplace injury.
Instead of simply raising wages, processing facilities should consider other benefits that may be attractive to the skilled labor they aim to retain. These can include retirement saving options, a more robust paid family leave plan, accessible medical insurance plans, and more.
Automation Bridges the Gap
A long-term solution to filling the labor gap is implementing automation in food processing. Automation can go a long way toward filling the labor gap and overcoming the skilled labor shortages in the food industry. This technology can not only boost efficiency, but also assist in the consistency and repeatability necessary in food production environments.
Automated equipment and robotics can perform a wide range of tasks, including food preparation, packaging, and quality control and analysis — and do it without experiencing fatigue or variability between batches. This technology can also track inventory and performance to provide valuable data insights for optimizing operations. For instance, fully automatic baggers ensure product weights are accurate, while robotic arms reliably stack pallet after pallet without any downtime. Vision inspection systems can also be used to scan packaged items for defects and other quality control issues.
Designed properly, automated solutions can both increase production while reducing risks for your existing workforce. While raising wages can serve as an immediate short-term solution, implementing automation sets up facilities for more long-term sustainability and growth. As production volumes change, automation allows processing plants to evolve with them.
Focusing on Employee Retention and Development
Another strategy for filling the labor gap is focusing on your existing employees. Food processing facilities that invest in additional automation can eliminate tasks that employees don’t want to do or are risky for them to perform, which allows the facility to have their employees focus on more value-add tasks.
Automation is also an extremely attractive consideration for skilled candidates. The technology gives workers more peace of mind at work, while providing them the opportunity to focus on managing and enhancing production processes, rather than physically operating all of the equipment.
Strategically implementing automated solutions as part of employee retention programs strengthens food safety programs while allowing facilities to increase efficiencies and overall production. Embracing automation can help facilities create high-value roles that attract new, top talent - and, perhaps most important, keep them for the long run.
Looking Ahead
While increased wages provide partial relief to food processing facilities experiencing labor pressure, automation can help processing facilities gain productivity, efficiency, and workplace safety in a sustainable way. These automated systems make high-volume food production efficient, even with ongoing hiring challenges. The food industry should see automation as a real solution to bridging labor gaps while upholding quality and safety standards across their operations.